For over a year we have been trying to adjust the joints of our functional sample. Unfortunately, Item’s standard joints as well as those provided by other manufacturers do not meet our requirements. That’s why we started designing our own. After joints manufactured using conventional 3-D printing processes and materials had failed because they did not exhibit the required strength, we tried to re-mill commercial joints to our needs. Sadly, these too were unstable…
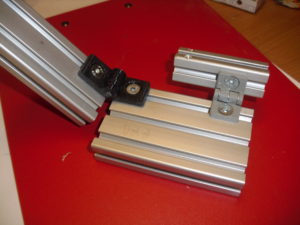
But what exactly is the problem? The above picture shows a joint mounted in a sample. The grey joint can only connect two profiles in parallel. And it’s doing that perfectly fine, however, for our frame we need a joint, which allows two profiles to be mounted end to end. This requires the locking nubs to rotated by 90°.
On our FB page we posted that we attended an introductory course in Autodesk 360 at SAXEED in Chemnitz. This software is free for small businesses and we used it to redesign our joints another time. Subsequently, Joseph from the Idea Workshop, who owns 2 3-D printers and has gained a lot of experience with a variety of materials, offered to manufacture the joints. After a brief test and a small adjustment, we had a whole swing of new joints to work with. Three hours later, all joints had been reground and detached from their support structure and, once the spacers and the split pins had been inserted, they were ready to be built into the frame. And just in time for the second public test this year: at short notice, we were invited to the 15th BVF Financial Congress to present our CompactChart. Thanks again to Anne from NrEins.de; your sample will be ready soon.
And again, we took a big step towards stability and reproducibility. Next, we will work on streamlining the design, which we will share with you at the end of February.
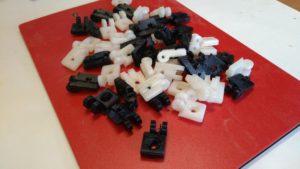
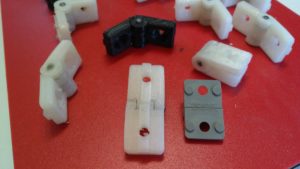